東莞UV噴油上光工藝常見問題及解決
1、白點與針孔現象
原因:涂布太薄或網紋輥過細;稀釋劑選用不當;表面粉塵較多或噴粉的顆粒太粗。
解決:選用合適網紋輥,增加涂層厚度;加入少量平滑助劑,采用參與反應的活性稀釋劑;保持表面清潔與環(huán)境清潔,不噴粉或少噴粉或選擇質量好的噴粉。
2、附著力差,涂不上或發(fā)花現象
原因:印刷品油墨表面產生晶化油、噴粉等,水墨中合調墨油及燥油過多;UV光油粘度太小或涂層太薄;涂膠網紋輥太細;光固化條件不合適;UV光油本身附著力差及印刷品材料的附著性差。
解決:消除晶化層,打毛處理或油脂或加入5%的乳酸;選擇與UV油工藝參數相匹的油墨輔材、或用布擦拭;使用粘度高的UV光油,加大涂布量;換用與該UV光油相匹配的網紋輥;檢查是否紫外光汞燈管老化,或機速不符,選擇合適的干燥條件;上底膠或更換特殊的UV光油或選擇表面性能好的材料。
3、氣泡現象
原因:所用UV油質量不高,UV油本身含有氣泡,多發(fā)生在用絲網上光中。
解決:換用質量高的UV油或將其靜置一段時間再用。
4、桔皮現象
原因:UV油粘度高,流平性差;涂布輥太粗不光滑且涂布量過大;壓力大小不均勻。
解決:降低粘度,加入流平劑及適當的溶劑;選用細的涂布輥和減少涂布量;調整壓力。
5、"麻點"現象
原因:油墨發(fā)生了晶化現象;表面張力值大,對墨層潤濕作用不好。
解決:在UV油中加入5%的乳酸,破壞晶化膜或除去油質或打毛處理;降低表面張力值,加入表面活性劑或表面張力值較低的溶劑。
6、殘留氣味大
原因:干燥不徹底,如光強度不足或非反應型稀釋劑過多;抗氧干擾能力差。
解決:固化干燥要徹底,選擇合適的光源功率與機速,減少使用噴油廠非反應型稀釋劑或不用它;加強通氣排氣系統。
7、光澤不好亮度不夠
原因:UV光油粘度太小,涂層太薄,涂布不均;印刷材料粗糙,吸收性太強;網紋輥過細,供油量太小;非參加干燥反應溶劑稀釋過度。
解決:適當提高UV光油粘度及涂布量,調整涂布機構使涂布均勻;選擇吸收性弱的材料,或先涂布一層底膠;加大網紋輥,提高供油量;減少乙醇等非反應稀釋劑的加入。
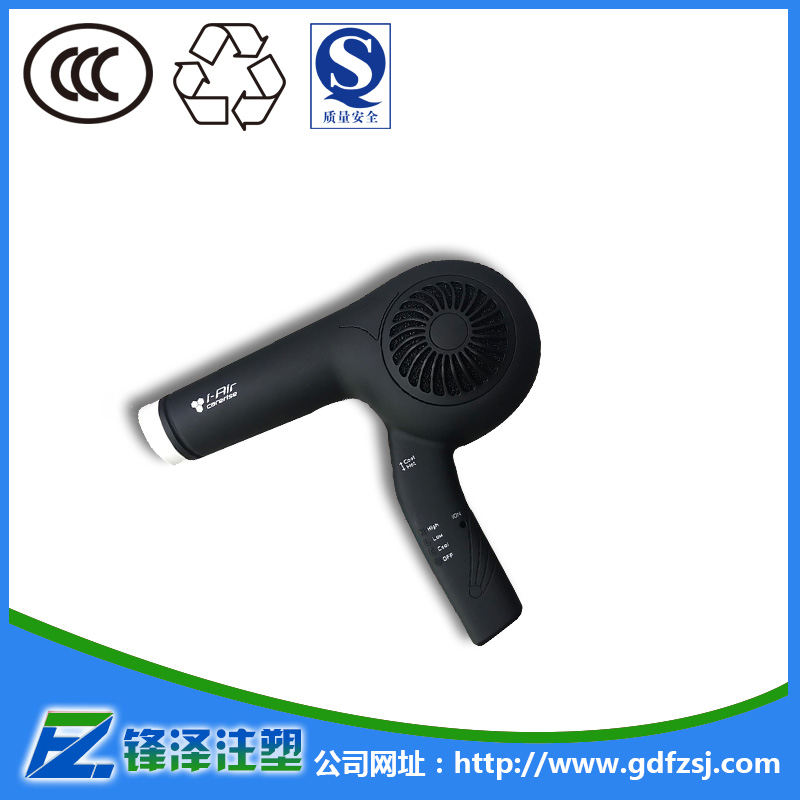
東莞UV噴油工藝
1.上料
操作者在工作臺面的上料區(qū)手工將半成品瓶蓋,瓶子等工件套在夾具上,通過輸送傳動鏈依次通過生產線的各個功能部件。
2.靜電除塵
因塑膠表面電荷積累和空氣灰塵存在帶電粒子,塑膠表面往往吸附大量塵埃,使用靜電除塵器在工作表面形成高壓負離子電場并用高壓空氣流吹工件表面,有效清除表面電荷和塵埃。
3.底涂
經過火焰處理的基材通過輸送傳動鏈進入噴房,噴房內的噴槍向其噴射涂料.同時基材受強制回轉系統的控制而產生自轉,使基材表面獲得均勻的涂層。
4. 快速低溫烘烤
底涂噴完后,基材即進入烘道調溫至60-70℃,烘烤1-2分鐘,溶劑揮發(fā)達到90%,涂料樹脂產生交聯反應,漆膜硬化。